- 29 november 2017
- | 5 min. leestijd
- | Bron: NPT Procestechnologie
DR. CHARLOTTE WILES KNOWS ABOUT MICRO REACTORS
Chemtrix is not an everyday, run-of-the-mill startup. It did not invent a smart gadget or find a small process improvement to settle in a tiny, previously unknown niche in the market. Yes, it did start out with a fairly simple discovery in reaction control but in just a few years, that idea was developed into a range of products which is already revolutionising the way chemistry is done. An interview with dr. Charlotte Wiles, CEO at Chemtrix BV.
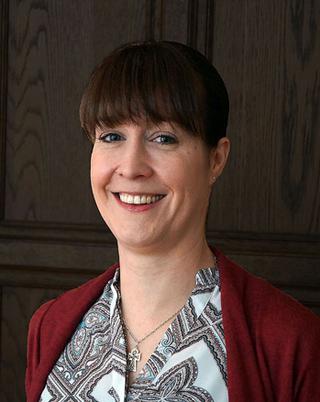
WHO IS DR. CHARLOTTE WILES?
Charlotte Wiles has been working in the field of micro reactor technology for more than 15 years. In 2003 she obtained her PhD at the University of Hull, entitled `Micro reactors in organic chemistry'.
This was followed by 5 years of post-doctoral research into the rapidly developing field of continuous flow synthesis. She has authored books, scientific papers and review articles on the subject. From 2008-2013 she worked at Chemtrix BV as CTO, designing and evaluating continuous flow reactor technology for use in both research and production purposes.
After that, she became the company's CEO, growing strategic partnerships with companies like 3M Technical Ceramics GmbH and DSM Fine Chemicals. Chemtrix is located at the Chemelot (www.chemelot.com) site in Geleen. It has offices and laboratories in Europe, US, China, India, Taiwan and Japan.
“Yes! About 15 years ago, in Hull, I worked as a PhD student under Professor Stephen Haswell and Paul Watts, where our group made small microreactors for analytical purposes (meant to detect very small amounts of chemicals). For that, you use organic reactions as sensors - like dye formation to produce a signal/colour indicating the presence of a substance. We wondered: if it works so quickly in these devices, couldn't you also use them to synthesize chemicals?"
Were there a lot of people involved?
“We started out as just a group of three PhD students and Post Docs, looking at proof of concept: could you actually manufacture chemicals in this way? As we couldn't buy any of the reactors, we had to make them ourselves. For that, we had to learn how to make them, and learn how to use them. It was a great journey and in three years we learned a lot about designing and making the reactors and finding out what you could and couldn't do with them."
And after that?
“We had lots of publications and case studies which got people interested, our supervisors from the university, and PhD sponsors like Novartis, Astra Zeneca and GSK. One of them said: 'Great results, but how do I replicate them?' There was only one reactor of each type in existence, so as a naïve PhD-student I said: 'You can take mine and try!' At that time, there was nothing commercially available we saw this as a hurdle for industrial uptake."
How did you actually make the first lab reactors?
“They consist of two glass plates, with channels, mixers, pre-heating and quenching areas etched into them using photolithography. The plates are then bonded together. The micro reactors can be heated or cooled by putting them on small, electronically controlled Peltier devices. And they are mounted in a small holder to make the necessary connections. Changing the pump rate and the reactant ratio provide more possibilities to change reaction time and other characteristics."
Dr. Charlotte Wiles: "We decided not to incorporate sensors in the reactor. This would involve deciding which ones to choose, and each brand of chemistry has its own sensor suppliers and interfaces. So these measurements take place off-line."
I don't see any sensors incorporated in the reactor?
“No, we decided not to. It would involve deciding which ones to choose, and each branch of chemistry has its own sensor suppliers and interfaces. So these measurements take place off-line. The user can use his own measuring equipment, apart from the reactor. And we maintain the reactor's flexibility."
What happened after these first reactors?
“Well, we met an entrepreneur from Enschede, Holland, from a firm called LioniX International, Dr Hans van den Vlekkert. He took a look at our reactors and said: “I can do that better." So we started working together. We made prototypes, adapting the size and then we did serial production. Our dream at that time was that the continuous flow reactor would become something like the round bottomed flask. Just a tool you pick from a drawer when you need to perform a reaction."
How did you go commercial?
“First we - the University, LioniX and Professor Paul Watts - did some basic research on the business opportunities. The results were looking good, so we decided to start a new venture together: Chemtrix BV. Actually, it was never intentional, Chemtrix grew out of the discovery. For many years we kept seeing ourselves more as scientists than entrepreneurs."
Dr. Charlotte Wiles: "We had to make the product usable in practical situations and then we developed the various sizes. We always had in mind that whatever you do in a lab, you must be able to scale it up to a manufacturing size."
How was the product developed?
“What followed was an engineering phase, together with LioniX International. We had to make the product usable in practical situations and then we developed the various sizes. We always had in mind that whatever you do in a lab, you must be able to scale it up to a manufacturing size. As a result, we also had to resort to different materials for the reactors, such as silicon carbide, a beautiful material for performing and controlling chemistry. Partnering with experts in glass and ceramic manufacturing allows Chemtrix BV to concentrate on designing the reactors and implementing them on various chemical processes."
The system looks so obvious, it shouldn't be hard to sell…
“Chemical sector innovates with the products it delivers but is an incredibly conservative sector when it comes to how those products are produced. There are some good reasons for that: in bulk chemistry it is the enormous historical investments that make it slow to change. In the pharmaceutical sector production is highly regulated so again change takes time you have to be very careful, obviously the FDA are vocal in their support for continuous manufacturing which has increased engagement. Chemtrix is about smaller, more flexible installations that can be installed for a dedicated production type or flexibly re-configured to deliver alternative products."
It is about money, then?
“As with all investments it is about ROI. A new technology can also mean a new business model and this takes time for an industry to adapt to. People understand payback time in the world they are used to, so we do trial work, demonstrations and training to deliver the needed proof for an emerging technology. It is not a catalogue product, but their use is becoming more common. Every day I wake up to e-mails from companies saying 'can you do this?' or 'have you done that before?' I love that."
WHY MICRO REACTORS?
Reactions in micro reactors take place in tiny channels, in a continuous flow. The advantages over large scale (batch) reactors are many and well documented. Mixing can be achieved within seconds and reaction conditions, such as reaction time, temperature, flow, pumped volumes and pressure, can be controlled and changed almost instantly. In many cases, micro reactors offer higher energy efficiency, reaction speed and yield, safety, reliability and scalability.
The high surface area to volume ratio (much higher than a batch reactor) enables almost instantaneous heating or cooling. The reaction temperature can even be raised above the solvent's boiling point, resulting in faster reactions and high reaction selectivity, so that less (potentially hazardous) intermediates will be formed.Scaling up production is easy, because the control, mixing and heat transfer properties are maintained.